-
Categories
-
Steel Pipe
-
Steel Profile
-
Steel Coil
-
USE
Structural steel pipe Fluid pipeShape
Square steel pipe Rectangular steel pipe Round steel pipe Shape tubeStandard
EN10210 EN10219 ASTM A500 ASTM A501 ASTM A53 ASTM A106 ASTM A572 ASTM A992 JIS G3466 AS/NZS 1163 CSA G40.20 CSA G40.21 API 5L API 5CTMaterial
Carbon steel pipe Alloy steel pipe Stainless steel pipeMolding Process
ERW steel pipe LSAW steel pipe Spiral welded steel pipe Seamless steel pipeTurface Treatment
Black steel tube Pre galvanzied steel tube Hot dip galvanized steel tube Zinc aluminum magnesium coating steel tubeSales Attributes
Sample list OEM ODM New arrival Basic style Star style -
-
Home / Galvanizing Process
Galvanizing Process
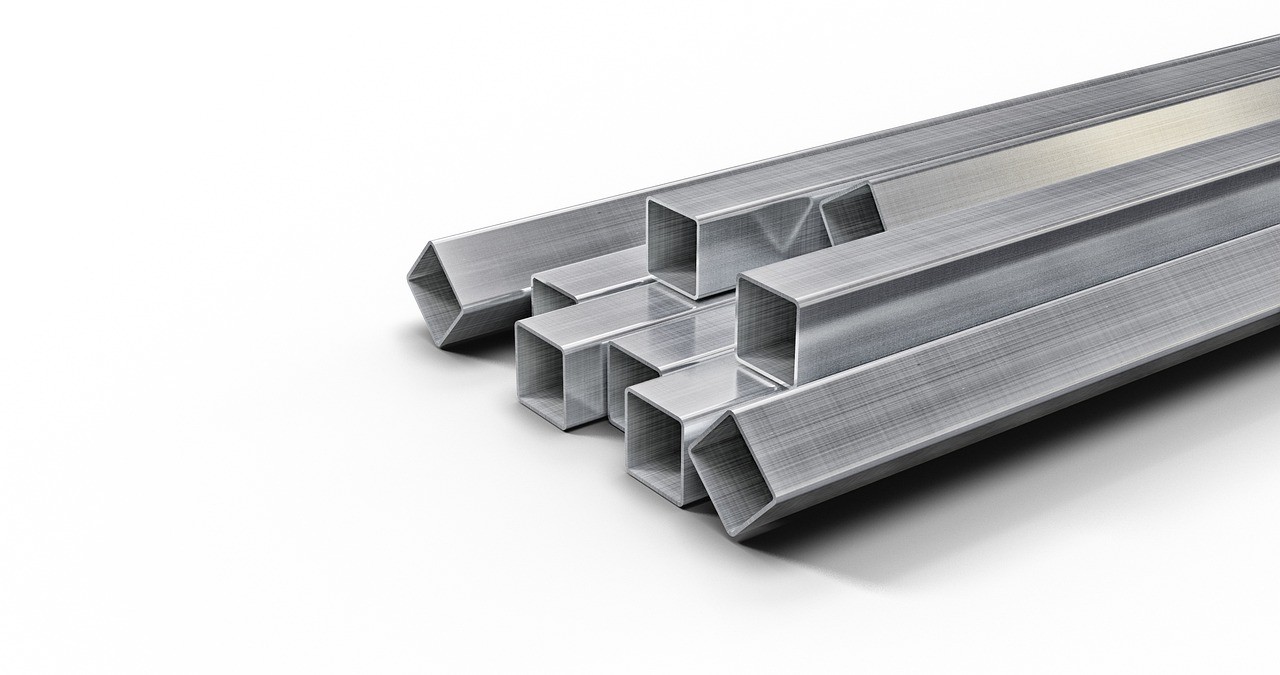
1.What Is The Galvanizing Process?
Yuantai Derun Steel Pipe Group currently has 26 hot-dip galvanizing production lines. The Hot-dip galvanization process generally refers to the process of putting black carbon steel pipes and pipe fittings into the zinc bath to coat the steel pipes or carbon steel pipe fittings with a layer of zinc. In recent years, with the rapid development of high-voltage transmission, transportation, and communication industries, the requirements for protection of steel parts have become increasingly high, and the demand for hot-dip galvanizing has also continued to increase.
2.Galvanizing Equipment Display
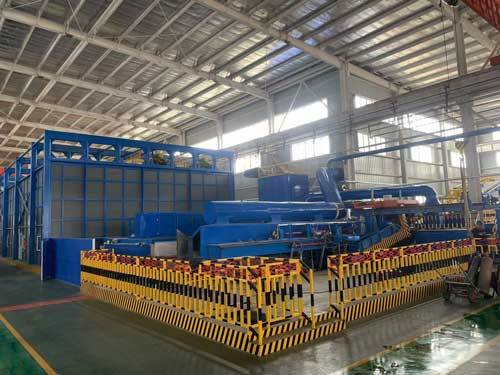
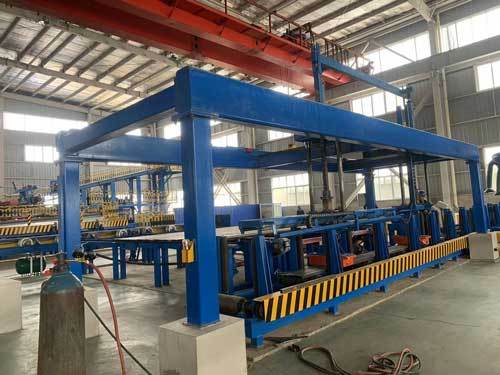

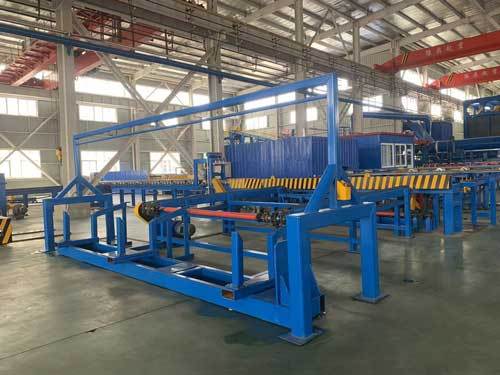
3.Protective Performance of Hot-dip Galvanized Layer
Usually, the thickness of the galvanized layer is 5-15 μ m. And the hot-dip galvanized layer is generally at 65 μ Above m, even up to 100 μ M. Hot dip galvanizing has good coverage ability, dense coating, and no organic inclusions. As we all know, the mechanism of zinc's resistance to atmospheric corrosion includes mechanical protection and electrochemical protection. Under atmospheric corrosion conditions, there are ZnO, Zn (OH) 2 and basic Zinc carbonate protective films on the surface of the zinc layer, which can slow down the corrosion of zinc to a certain extent. If this protective film (also known as white rust) is damaged, a new film will be formed. When the zinc layer is severely damaged and endangers the iron substrate, zinc provides electrochemical protection to the substrate. The standard potential of zinc is -0.76V, and the standard potential of iron is -0.44V. When zinc and iron form a micro battery, zinc is dissolved as the anode, and iron is protected as the cathode. Obviously, hot-dip galvanizing has better atmospheric corrosion resistance to the base metal iron than electrogalvanizing.
4.Formation Process Of Hot-dip Galvanized Layer
The formation process of hot dip galvanized layer is the process of forming an iron zinc alloy between the iron substrate and the outermost pure zinc layer. The iron zinc alloy layer is formed on the surface of the workpiece during hot dip plating, which allows for good bonding between the iron and pure zinc layers. The process can be simply described as: when the iron workpiece is immersed in molten zinc liquid, zinc is first formed at the interface α Iron (body core) solid melt. This is a crystal formed by the dissolution of zinc atoms in the solid state of the matrix metal iron. The two metal atoms are fused, and the attraction between the atoms is relatively small. Therefore, when zinc reaches saturation in the solid melt, the two elemental atoms of zinc and iron diffuse with each other, and the zinc atoms that diffuse (or infiltrate) into the iron matrix migrate in the matrix lattice, gradually forming an alloy with iron. The iron that diffuses into the molten zinc liquid forms an intermetallic compound FeZn13 with zinc, which sinks into the bottom of the hot dip galvanizing pot, forming zinc slag. When the workpiece is removed from the zinc immersion solution, a pure zinc layer is formed on the surface, which is a hexagonal crystal. Its iron content shall not exceed 0.003%.
5.Hot Dip Galvanizing Process And Related Instructions
5.1 Process
Workpiece → degreasing → water washing → acid washing → water washing → immersion in auxiliary plating solvent → drying and preheating → hot dip galvanizing → finishing → cooling → passivation → rinsing → drying → inspection
5.2 Process Description
(1) Defatting
Chemical degreasing or water-based metal degreasing cleaning agents can be used to degrease the workpiece until it is completely soaked in water. (2) Pickling can be carried out with H2SO4 15%, thiourea 0.1%, 40~60 ℃ or HCl 20%, hexamethylene tetramine 1~3g/L, 20~40 ℃. Adding corrosion inhibitors can prevent excessive corrosion of the matrix and reduce hydrogen absorption of the iron matrix.
Poor degreasing and pickling treatment can result in poor adhesion of the coating, failure to apply zinc or detachment of the zinc layer.
(3) Dipping auxiliary plating agent
Also known as a binder, it can maintain a certain degree of activity of the workpiece before immersion, in order to enhance the bonding between the coating and the substrate. NH4Cl 15%~25%, ZnCl2 2.5%~3.5%, 55~65 ℃, 5-10 minutes. To reduce the volatilization of NH4Cl, glycerol can be added appropriately.
(4) Drying preheating
In order to prevent deformation of the workpiece during immersion plating due to a sharp increase in temperature, remove residual moisture, and prevent the occurrence of zinc explosion, resulting in zinc liquid splashing, the preheating temperature is generally 120~180 ℃.
(5) Hot dip galvanizing
It is necessary to control the temperature of the zinc solution, the immersion time, and the speed at which the workpiece is removed from the zinc solution. Low temperature, poor fluidity of zinc solution, thick and uneven coating, easy to produce sagging, and poor appearance quality; High temperature, good fluidity of zinc liquid, easy detachment of zinc liquid from the workpiece, reduced sagging and wrinkling, strong adhesion, thin coating, good appearance, and high production efficiency; However, if the temperature is too high, the workpiece and zinc pot iron are severely damaged, resulting in a large amount of zinc slag, which affects the quality of the zinc dipping layer, resulting in high zinc consumption and even inability to apply zinc. At the same temperature, the immersion time is long and the coating is thick. When different temperatures require the same thickness, high-temperature immersion plating requires a long time. In order to prevent high-temperature deformation of workpieces and reduce zinc slag caused by iron loss, general manufacturers use 450~470 ℃ for 0.5~1.5min. Some factories use higher temperatures for large workpieces and cast iron castings, but they need to avoid the temperature range of peak iron loss. In order to improve the flowability of the hot dip plating solution at lower temperatures, prevent excessive coating thickness, and improve the appearance of the coating, pure aluminum of 0.01% to 0.02% is often added. Aluminum needs to be added in small quantities multiple times.
(6) Organize
After plating, the main task of organizing the workpiece is to remove residual zinc and zinc nodules on the surface, which can be done using vibration or manual methods.
(7) Passivation
The purpose is to improve the atmospheric corrosion resistance of the workpiece surface, reduce or extend the appearance time of white rust, and maintain a good appearance of the coating. They are passivated with Chromate and dichromate, such as Na2Cr2O7 80 ~ 100g/L, sulfuric acid 3 ~ 4ml/L.
(8) Cooling
Generally, water cooling is used, but the temperature should not be too low to prevent the workpiece, especially the casting, from cracking the matrix structure due to quenching and shrinkage.
(9) Inspection
The appearance of the coating is bright, delicate, and free from sagging and wrinkling. The thickness inspection can be carried out using a coating thickness gauge, which is a relatively simple method. The coating thickness can also be obtained by converting the zinc adhesion amount. The bonding strength can be achieved by using a bending press to bend the sample at 90-180 °, and there should be no cracks or peeling of the coating. It can also be inspected by striking with a heavy hammer.
Chemical degreasing or water-based metal degreasing cleaning agents can be used to degrease the workpiece until it is completely soaked in water. (2) Pickling can be carried out with H2SO4 15%, thiourea 0.1%, 40~60 ℃ or HCl 20%, hexamethylene tetramine 1~3g/L, 20~40 ℃. Adding corrosion inhibitors can prevent excessive corrosion of the matrix and reduce hydrogen absorption of the iron matrix.
Poor degreasing and pickling treatment can result in poor adhesion of the coating, failure to apply zinc or detachment of the zinc layer.
(3) Dipping auxiliary plating agent
Also known as a binder, it can maintain a certain degree of activity of the workpiece before immersion, in order to enhance the bonding between the coating and the substrate. NH4Cl 15%~25%, ZnCl2 2.5%~3.5%, 55~65 ℃, 5-10 minutes. To reduce the volatilization of NH4Cl, glycerol can be added appropriately.
(4) Drying preheating
In order to prevent deformation of the workpiece during immersion plating due to a sharp increase in temperature, remove residual moisture, and prevent the occurrence of zinc explosion, resulting in zinc liquid splashing, the preheating temperature is generally 120~180 ℃.
(5) Hot dip galvanizing
It is necessary to control the temperature of the zinc solution, the immersion time, and the speed at which the workpiece is removed from the zinc solution. Low temperature, poor fluidity of zinc solution, thick and uneven coating, easy to produce sagging, and poor appearance quality; High temperature, good fluidity of zinc liquid, easy detachment of zinc liquid from the workpiece, reduced sagging and wrinkling, strong adhesion, thin coating, good appearance, and high production efficiency; However, if the temperature is too high, the workpiece and zinc pot iron are severely damaged, resulting in a large amount of zinc slag, which affects the quality of the zinc dipping layer, resulting in high zinc consumption and even inability to apply zinc. At the same temperature, the immersion time is long and the coating is thick. When different temperatures require the same thickness, high-temperature immersion plating requires a long time. In order to prevent high-temperature deformation of workpieces and reduce zinc slag caused by iron loss, general manufacturers use 450~470 ℃ for 0.5~1.5min. Some factories use higher temperatures for large workpieces and cast iron castings, but they need to avoid the temperature range of peak iron loss. In order to improve the flowability of the hot dip plating solution at lower temperatures, prevent excessive coating thickness, and improve the appearance of the coating, pure aluminum of 0.01% to 0.02% is often added. Aluminum needs to be added in small quantities multiple times.
(6) Organize
After plating, the main task of organizing the workpiece is to remove residual zinc and zinc nodules on the surface, which can be done using vibration or manual methods.
(7) Passivation
The purpose is to improve the atmospheric corrosion resistance of the workpiece surface, reduce or extend the appearance time of white rust, and maintain a good appearance of the coating. They are passivated with Chromate and dichromate, such as Na2Cr2O7 80 ~ 100g/L, sulfuric acid 3 ~ 4ml/L.
(8) Cooling
Generally, water cooling is used, but the temperature should not be too low to prevent the workpiece, especially the casting, from cracking the matrix structure due to quenching and shrinkage.
(9) Inspection
The appearance of the coating is bright, delicate, and free from sagging and wrinkling. The thickness inspection can be carried out using a coating thickness gauge, which is a relatively simple method. The coating thickness can also be obtained by converting the zinc adhesion amount. The bonding strength can be achieved by using a bending press to bend the sample at 90-180 °, and there should be no cracks or peeling of the coating. It can also be inspected by striking with a heavy hammer.
Product
- Square Steel Pipe
- Rectangular Steel Pipe
- Round Steel Pipe
- Special Shaped Steel pipe
- LSAW Steel Pipe
- Zinc aluminium magnesium coating steel pipe
- Galvanized Steel Pipe
- ERW steel pipe
- Seamless steel pipe
- Spiral steel pipe
- LINE PIPE OCTG
- Ship Building Steel Pipe
- Stainless steel pipe
- Steel coil
- C channel
- Z channel
- Photovoltaic bracket
Reach us for
Please send your message to us
Yuantai team has over 21 years of experience in steel pipe project applications, specializing in the production, manufacturing, and customization of square rectangular, and circular steel pipes. Warmly welcome project procurement managers, individual owners, designers, and overall sellers, etc. Write down your requirements and receive professional quotes and technical support.
- Name
- Tel
- *Title
- *Content
- Upload
- Only supports .rar/.zip/.jpg/.png/.gif/.doc/.xls/.pdf, maximum 20MB.
- Address
Copyright © 2025 TIANJIN YUANTAI DERUN STEEL PIPE MANUFACTURING GROUP CO., LTD. Support By BEE Cloud