A Manufacturing Method for Square Rectangular Steel Pipe with Corner Thickening and Cold Hot Composite Forming
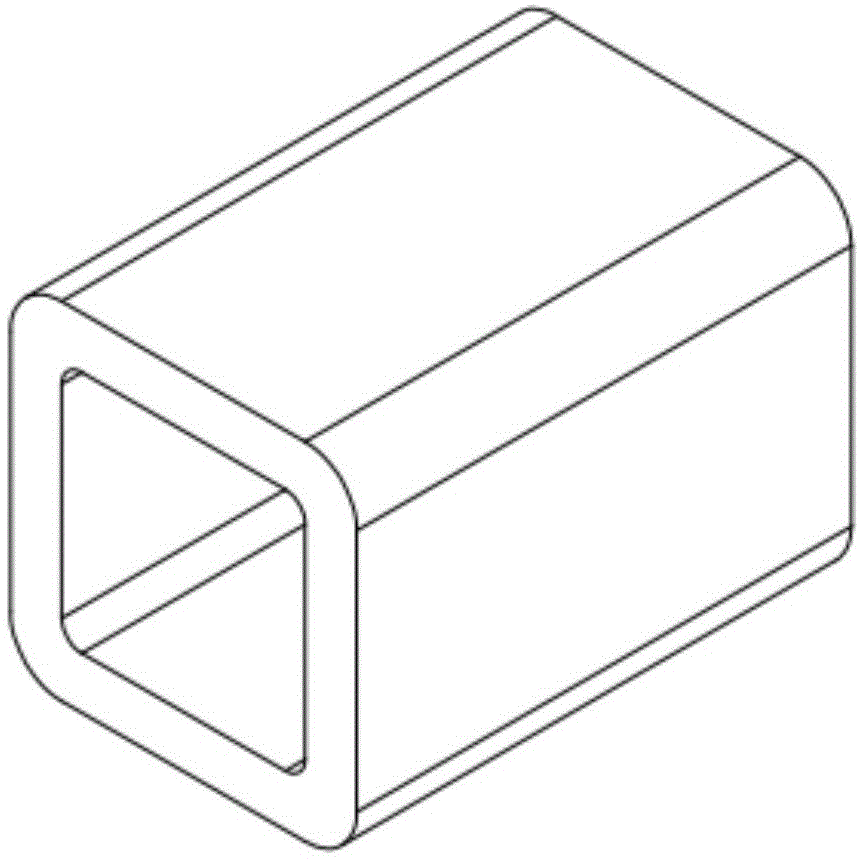
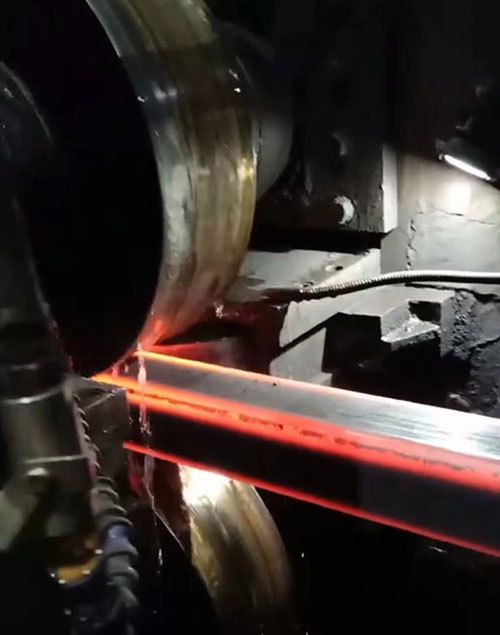
Background technology:
Nowadays, more and more people are pursuing lightweight, and square tube is the carrier that promotes the development of lightweight. For example, in steel structures, square tube can reduce by about 80% compared to the original brick concrete structure due to its own structural characteristics. At the same time, it has high yield strength, large bending section modulus, overlapping shear and centroid, good torsional performance, and fast construction; Compared to other types of steel, such as H-beams and circular tubes, square rectangular tubes have outstanding advantages in comprehensive performance and are known as the best material for steel structural columns.
However, the square tube currently used, due to its traditional cold bending forming process, will experience secondary work hardening effects during the processing, especially at the corners of the square tube, where residual stress is significant and the radius of the corners is large, resulting in a reduction in thickness. This greatly restricts the use of square tubes. In high-rise buildings, traditional cold formed square tubes cannot be used as the main material, At the same time, the large rounded corners also weaken the welding performance of square tube.
Technical implementation elements:
To address the defects in the corners of traditional cold-formed square steel pipes, this utility model proposes a square rectangular steel pipe formed by thickening the corners and combining cold and hot forming. Introducing hot forming technology, namely local induction heating technology, into traditional roll bending forming processes. High temperature can not only reduce the forming force of materials, but also improve their formability; And it can eliminate residual stress and possible cracking caused by work hardening. At the same time, the corner contour of the square steel pipe formed by cold and hot composite forming is dense, with a small inner and outer corner radius, and the corner angle is close to 90 °, accompanied by corner thickening.
The purpose of this utility model is to provide a square rectangular steel pipe formed by corner thickening and cold hot composite forming.
The outer corner radius of the square rectangular steel pipe meets the following conditions:
When t ≤ 6mm, 0<R<2.0t; Preferably 0<R<1.5t; More preferably 0<R<0.5t;
When 6<t ≤ 10mm, 0<R<2.5t; Preferably 0<R<2.0t; More preferably 0<R<0.75t;
When t>10mm, 0<R<3.0t; Preferably 0<R<2.5t; Preferably, 0<R<1.0t.
Among them, t is the wall thickness of the square rectangular steel pipe; R is the outer radius of the four corners of a square rectangular steel pipe.
The corner wall thickness of the square rectangular steel pipe is between 1.0t and 1.8t, preferably between 1.0t and 1.2t.
Preferred:
The cross-sectional circumference of a single welded square rectangular steel pipe is 80mm-4800mm;
The straight wall thickness of a single welded square rectangular steel pipe is 6mm-70mm;
The perimeter of the double welded square rectangular steel pipe section is 1600mm~9600mm;
The straight wall thickness of double welded square rectangular steel pipes is between 20mm and 80mm.
The preparation method of the square rectangular steel pipe formed by the corner thickening cold hot composite forming of this utility model is as follows:
Including:
1) Introduce the pre finished square rectangular steel pipe into the subsequent production system through rolling smoothly and symmetrically;
2) Conduct local heating on the four corners of the rectangular steel pipe through an induction coil;
3) The square rectangular steel pipes heated at the corners are sequentially fed into the precision forming unit, and each forming unit rolls and forms the four corners of the square steel pipes; At the same time, by controlling the difference in the rotational speed of the rolls during the rolling process of each adjacent unit, the square rectangular steel pipe is subjected to thermal tension between the adjacent units, eliminating redundant deformation during the thermal finishing process;
4) Control cooling of square steel pipes through a water cooling system to ensure the strength performance of the finished square steel pipes, followed by air cooling;
5) Cut the finished rectangular steel pipe.
Among them, it is preferred to:
Step (2), heating temperature range: 750 ℃~1100 ℃; The heating time shall not be less than 15 seconds.
Step (3): Heat the four corners of the rectangular steel pipe through the flame spray gun insulation system to ensure a constant temperature during the thermal finishing stage and prevent its temperature from decreasing;
The temperature control range is 700~950 ℃.
Step 3), for each adjacent precision forming unit, the difference in roller diameter is taken as 1-5mm.
Step (3), the number of precision forming units is 5, with 5 precision forming machines