Why is there residual stress in rectangular tubes?
Why is there residual stress in rectangular tubes?
Rectangular tube is a widely used closed end steel. Compared with circular tubes of the same cross-sectional area, it has advantages such as high strength, large modulus of bending section, easy assembly, stability, and aesthetics. It is widely used in industries such as vehicles, subways, and shipbuilding. Especially in the construction industry, large-sized square rectangular pipes have become the main load-bearing structural components in steel structures. As a typical closed end steel, square rectangular tubes leave residual stress during each machining process during the manufacturing process. The different processing techniques of square tubes inevitably result in varying degrees of residual stress.
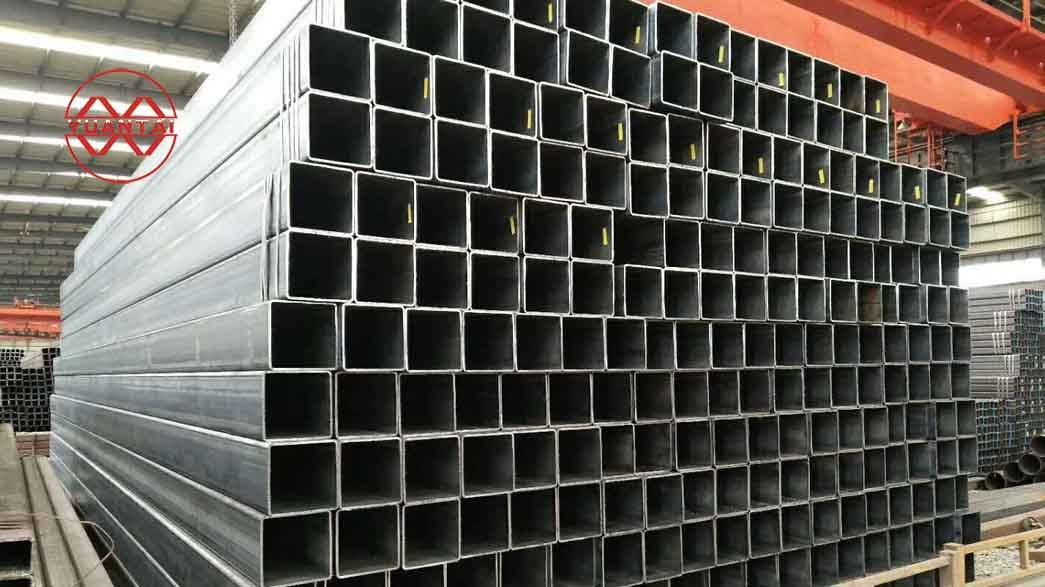
There are two methods for forming cold-formed square tubes: "direct square forming" and "circular square forming". Scholars from North China University of Technology, in order to study the different effects of forming process on products 100mm×100mm×6mm The residual stresses in various parts of the square tube with two forming processes of 6mm and Q235 material were measured using the drilling method, and the microstructure at the weld seam was observed. The research results indicate that different forming processes have a significant impact on the distribution of longitudinal residual stress, and the residual stress at the weld seam is large. During the process of "rounding into square", a large welding pressure is applied to make the width of the welding heat affected zone smaller than that under the "direct square" process conditions, and to control the growth of austenite grains. After cooling, relatively small and uniform grains are obtained.