How Is Steel Pipe Made?
How was a steel pipe born? Do you also have this question. Today, we will take you to briefly understand the current mainstream steel pipe production process. The current mainstream steel pipes are divided into seamless steel pipes and welded steel pipes.
1. How Is Seamless Steel Pipe Made?
1.1 Manufacturing Process Of Hot Extruded Seamless Steel Pipes
Firstly, the initial state of all raw materials for the production of seamless steel pipes is round billets, and hot extruded seamless steel pipes are no exception. These round steel billets that have passed the inspection are sequentially fed into the heating furnace for heating.
The second step is perforation, and the heated steel billet needs to be perforated.
The third step is hot extrusion. After induction heating, the perforated pipe blank enters the hot extrusion process in sequence, and the extruded blank now has the shape of a seamless steel pipe.
In the fourth step, the seamless steel pipe that has already taken shape undergoes secondary heat treatment and straightening processes to obtain the finished seamless steel pipe.
The specific production process flow of seamless tube hot extrusion is shown in the following figure:
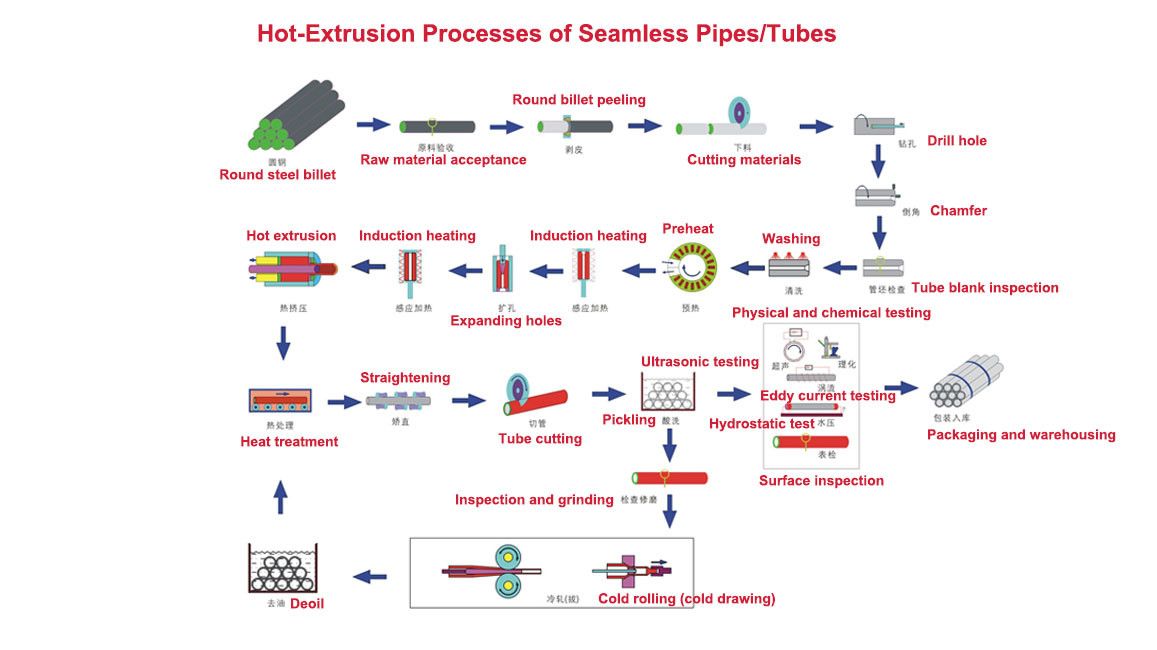
1.2 Manufacturing Process Of Cold Drawn Seamless Pipes
After seeing the manufacturing process of hot extruded seamless steel pipes, let me take you to see the manufacturing process of cold-rolled (cold drawn) seamless steel pipes again. The circular tube blank first needs to be pierced by two roll continuous rolling, and then it needs to enter the steel rolling mill for fixed diameter rolling. After surface pickling, the round tube needs to undergo precise cold drawing treatment by the cold drawing machine, and the round tube needs to undergo secondary heat treatment. Then it enters the straightening machine, and after the straightness of the seamless round pipe is corrected, it is sent to the pipe cutting machine. In this way, a cold drawn seamless pipe is formed, and finally, the steel pipe is inspected and marked for storage. Visually, cold drawn seamless steel pipes are shorter than hot-rolled seamless steel pipes. The wall thickness of cold drawn seamless steel pipes is generally smaller than that of hot-rolled seamless steel pipes, but the surface looks brighter than hot-rolled seamless steel pipes. The surface is not so rough, and there are not too many burrs at the ends.
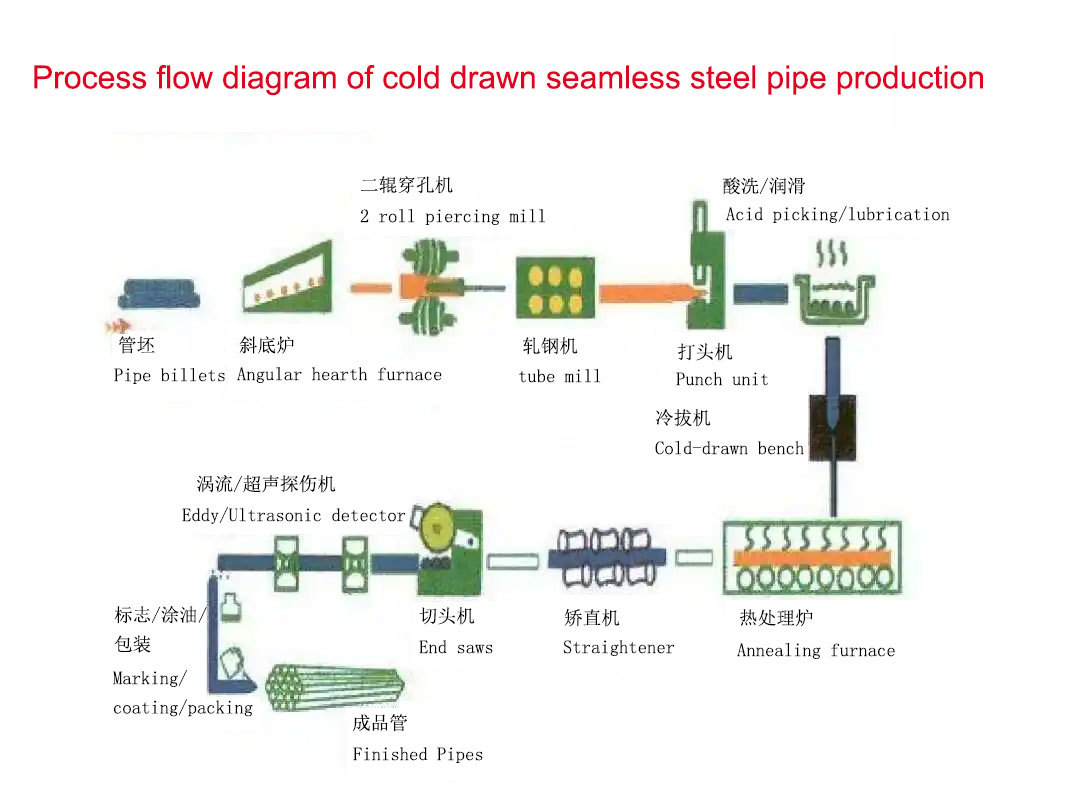
2. Manufacturing Process Of A Welded Steel Pipe
How is a welded steel pipe manufactured and produced by a factory? Firstly, let's take a look at several mainstream production methods for welded steel pipes. Normally, welded steel pipes can be divided into three categories based on different welding methods, namely ERW steel pipes, LSAW steel pipes, and SSAW steel pipes. Let me take you to briefly understand their respective manufacturing processes.
2.1 Manufacturing Process Of Erw Steel Pipes
Firstly, the raw material for producing ERW steel pipes is steel coils. The first step is to open and straighten the steel coil, and then cut and weld the edges of the steel coil.
The second step is roller cold forming, where the steel coil is gradually rolled into a circular or square shape. Then, tighten the edges of the formed round or square tube and perform high-frequency resistance welding. Remove the welded round or square tube from the weld seam.
The third step is to remove the round or square pipes from the weld seam and cool them with water, then perform diameter straightening, sawing, testing, marking, and storage. A ERW steel pipe was manufactured like this. As shown in the figure.
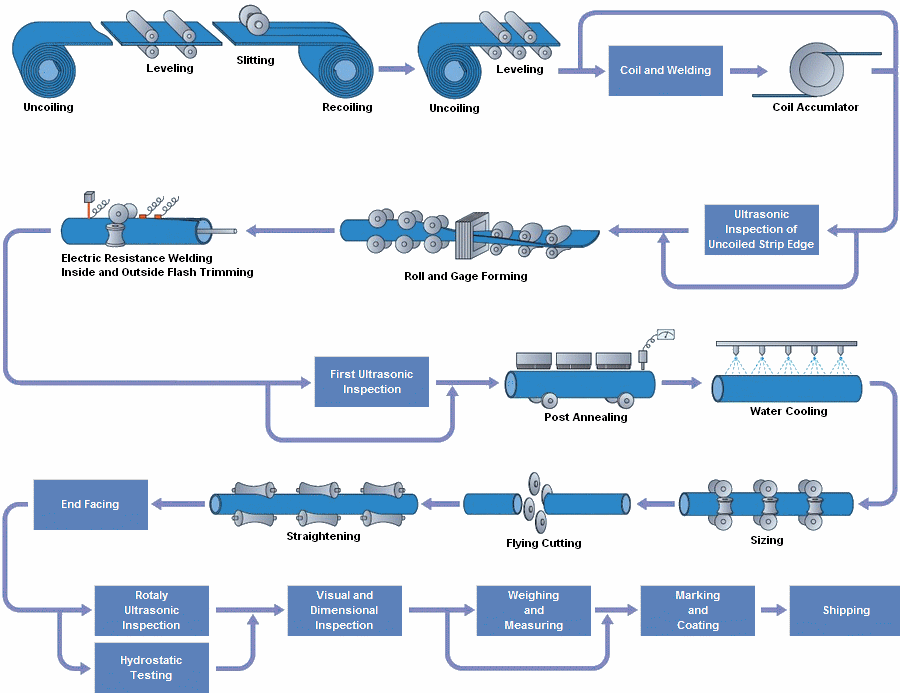
2.2 Manufacturing Process Of LSAW Steel Pipes
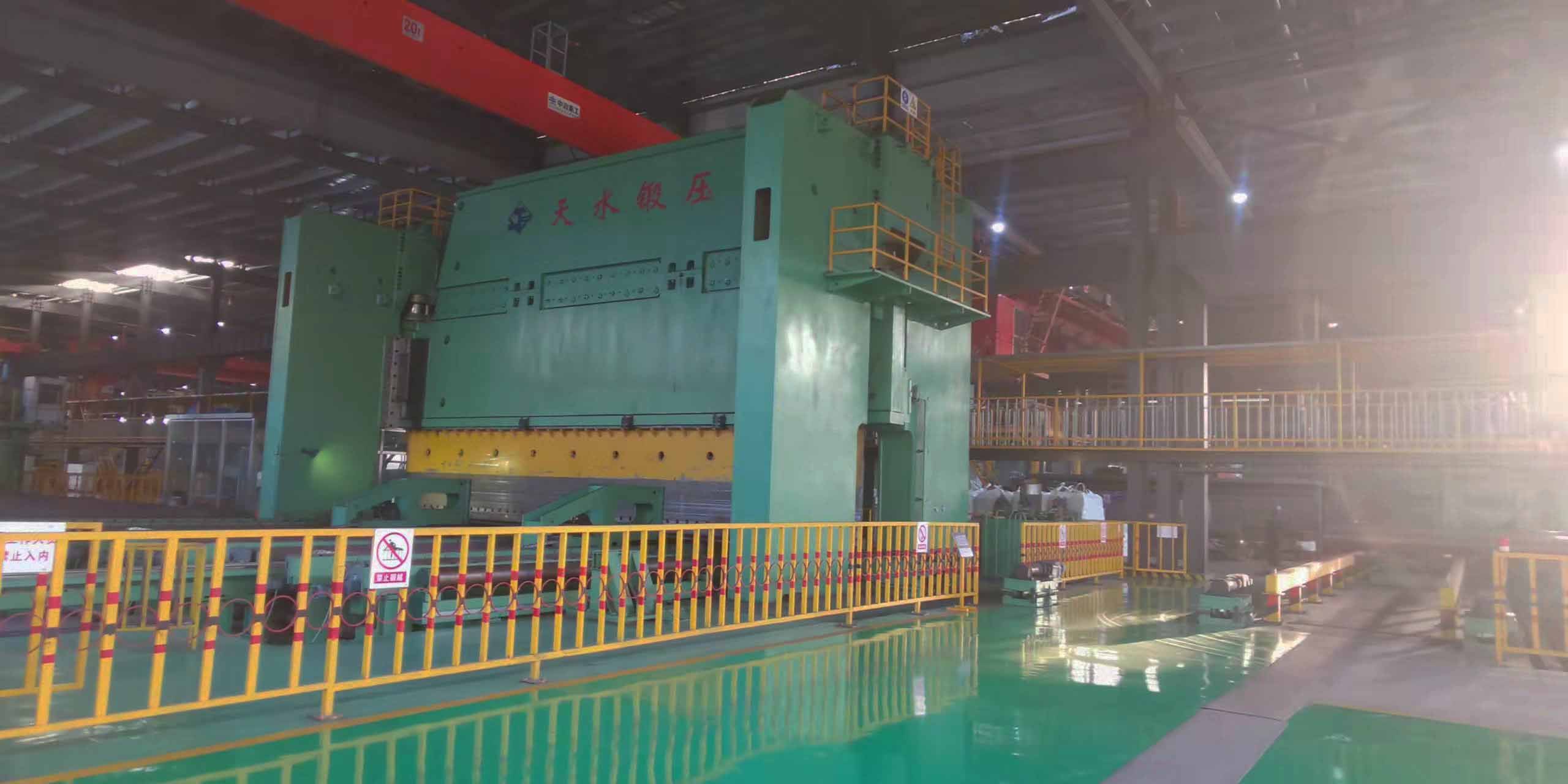
How was an LSAW steel pipe born? With this question in mind, I will take you to a brief understanding.
Firstly, the raw materials of LSAW steel pipes are different from those of ERW steel pipes. The raw materials of LSAW steel pipes are steel plates that have undergone strict testing and are qualified. The thickness of these steel plates can be customized by users, with a selection range of steel plate thickness from 6mm to 60mm. The first process that these steel plate raw materials need to undergo is edge cutting, which is prepared in advance for the welding below, because the edges of the cut steel plate leak out of the new steel plate surface, making it easier to weld.
The second step is to perform a pre bending process on the steel plate after the trimming is completed. The edges of the two originally flat steel plates are pre bent to ensure a smoother welding process.
The third step is to slowly feed the pre bent steel plate into the heavy-duty JCOE forging machine. At room temperature, the forging machine first rolls the steel plate into a "J" shape, then into a "C" shape, and finally into an "O" shape before sending it to the next process.
The fourth step, we call it "pre welding". The pre welding unit can pre weld the semi-finished product rolled into an "O" shape. This pre welding is to align the edges of the "O" shaped semi-finished product, perform pre welding treatment, and then weld the arc plate to prepare in advance for the next process.
Step 5, internal welding. The semi-finished product after pre welding treatment is sent to the internal welding machine for welding inside the weld seam.
Step 6, external welding. After the internal welding is completed, the semi-finished product is cleaned with welding slag and sent to the external welding machine for external welding.
Step 7, detection. After removing the welding arc plate, the LSAW steel pipe has already taken shape, and ultrasonic testing and X-ray testing are essential. Inspectors will conduct various non-destructive tests on the weld seam, and after passing the tests, it will be sent to the next process.
Step 8, sizing. After passing the inspection, the LSAW steel pipe is sent into the sizing equipment for size correction.
Step 9, flame flat mouth.
Step 10, water pressure test.
Step 11, ultrasonic testing and X-ray testing of welds. This is the second inspection conducted, which can ensure the quality of LSAW steel pipe welds. After passing the inspection, it is sent to the next step.
Step 12, polish the weld seam at the end of the pipe to remove any excess weld seam and make the pipe smoother.
Step 13, chamfering. The polished LSAW steel pipe is fed into the chamfering machine, and this step can be used to bevel or flatten the pipe end of the LSAW pipe. These are all executed according to the wishes of each steel pipe seller.
Step 14, magnetic particle inspection.
Step 15: Weigh and measure the length, perform visual inspection, and spray paint and label.
Step 16, finished product inspection. After the LSAW steel pipe is sprayed with the label, the final finished product inspection is also carried out. The fully qualified LSAW pipes are finally packaged and stored.
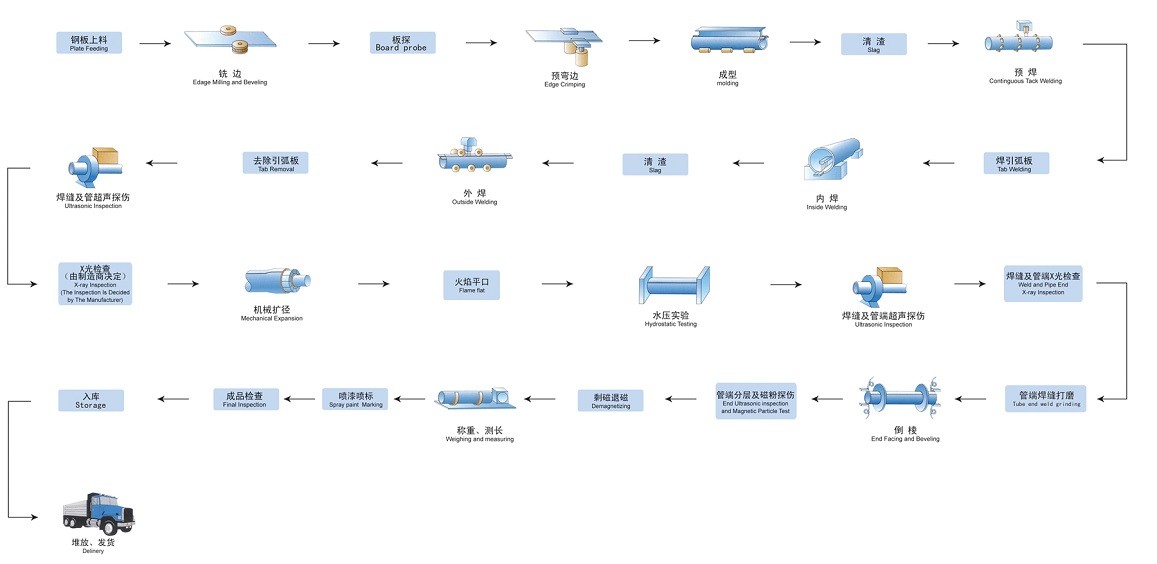
2.3 Manufacturing Process Of Spiral Welded Pipes
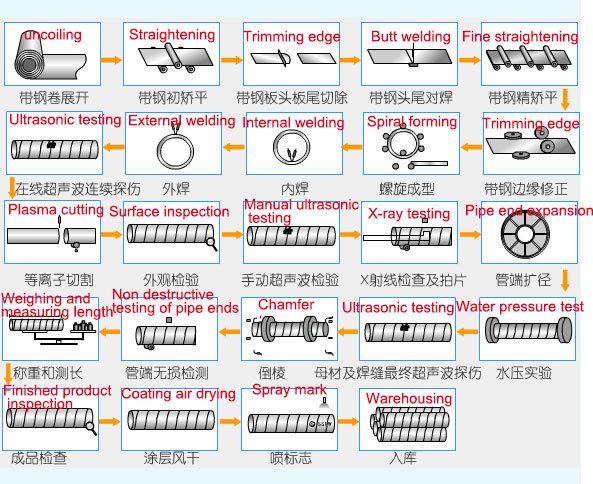
How is a spiral welded steel pipe manufactured? Similarly, let me give you a brief understanding.
Firstly, the raw material for spiral welded steel pipes is also steel coils, which is similar to the raw material for ERW steel pipes. The thickness of the steel coil determines the thickness of the spiral welded pipe after forming. The engineer has already specified the thickness of the steel coil in advance when ordering materials. Before the steel coil enters the unit, a strict quality inspection process must be carried out, which will not be repeated here. The first step in spiral welded pipe production is also to open the coil, slowly unfold the steel coil, straighten it, cut off the edges of the steel coil, and perform butt welding on the coil plate joint. The raw materials of the welded steel coil enter the next stage.
The second step is to trim the edges of the steel strip, and then the spiral forming can be awakened. After forming, the edges of the steel coil should be tightly aligned, and the internal weld seam should be welded first before the external weld seam.
The third step is online continuous ultrasonic testing.
Step 4, steel pipe cutting.
Step 5: Appearance inspection of steel pipes, manual ultrasonic testing, X-ray testing, and photo taking.
Step 6, expand the pipe end.
Step 7, Water Pressure Test
Step 8, final ultrasonic testing of the base material and weld seam.
Step 9, non-destructive testing of the pipe end.
Step 10, weigh and measure the length.
Step 11, air dry the coating.
Step 12, spray the logo.
Step 13, enter the warehouse.
3. Manufacturing Process Of An Alloy Steel Tube
How are alloy steel pipes produced? You may also have such questions. The following will take you a brief understanding of alloy steel pipe manufacturing understanding.
The production process of alloy pipe is mainly divided into raw material preparation, heat treatment, extrusion, cold drawing, annealing and inspection.
The Specific Production Process Of Alloy Pipe Is As Follows:
Billet Preparation ⇨ Ring Furnace Preheating ⇨ High Pressure Water Phosphorus Removal ⇨ Lubricant Coating on Inner and Outer Surfaces ⇨ Vertical Piercing (Expanding) Machine Piercing (Expanding) ⇨ Re-heating of Hollow Billet ⇨ High Pressure Water Phosphorus Removal ⇨ Lubricant on Inner and Outer Surfaces ⇨ Horizontal Extruding Machine Extruding ⇨ Diameter Setting (Reducing) Machine Diameter Setting (Reducing) ⇨ Walking Cold Bed Cooling (Water Cooling or Air Cooling) ⇨ Removal of Iron Oxide Skin and Lubricants ⇨ Roller Straightening Machine Straightening ⇨ Cutting of Pipes and Processing of Pipe Ends ⇨ Surface and Tolerance Inspection and Performance Test ⇨ Spraying of Marks and Packaging Into Warehouses
4. A Stainless Steel Tube Production Process
How is stainless steel tube produced? Not much to say, on the dry goods.
First of all, the raw material of stainless steel pipe preparation, stainless steel pipe raw material is stainless steel plate or stainless steel master batch, usually choose 304, 316 or 321 stainless steel as raw materials, of which 304 stainless steel is the most widely used, with good toughness, corrosion resistance, easy to process and other characteristics. In the selection of materials, but also pay attention to the size and thickness of the stainless steel plate and master batch, to meet customer requirements.
The second step, pipe making. Tube manufacturing is the core link of stainless steel tube production. Stainless steel pipe is divided into two kinds of seamless steel pipe and welded steel pipe (as shown in the figure), seamless stainless steel pipe is manufactured by hot rolling or cold drawing process, while welded stainless steel pipe is manufactured by welding process.
The manufacturing process of seamless stainless steel pipe includes: round steel ⇒ re-inspection ⇒ cutting ⇒ centering ⇒ peeling ⇒ heating ⇒ piercing ⇒ inspection ⇒ pickling ⇒ surface inspection ⇒ lubrication and drying ⇒ cold rolling (cold drawing) ⇒ de-oiling ⇒ solution heat treatment (annealing) ⇒ straightening ⇒ finished product testing (including: process performance, physical and chemical testing, hydraulic testing, non-destructive testing, corrosion testing) ⇒ marking ⇒ packaging ⇒ shipment, and in the following figure, it is the stainless steel seamless steel pipe The following diagram shows the production process of seamless stainless steel pipe.
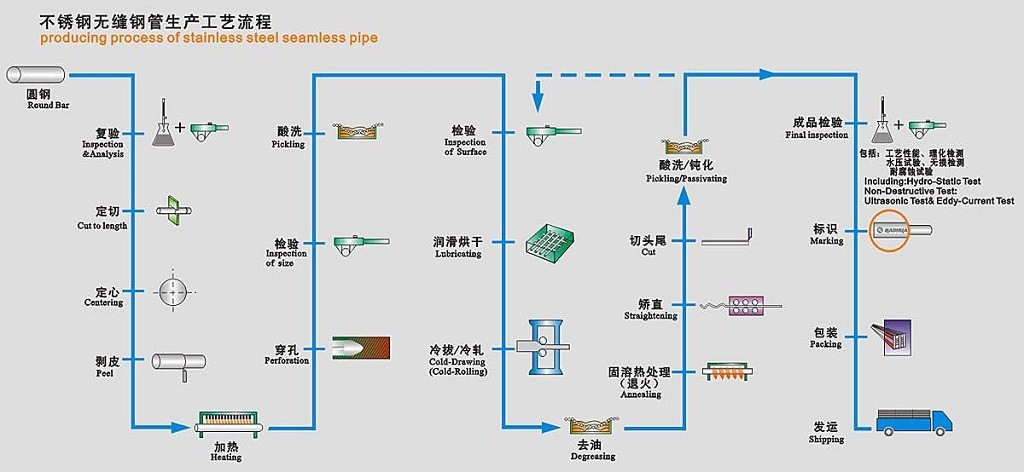
The manufacturing process of welded stainless steel pipe includes: plate inspection ⇒ uncoiling ⇒ cutting head butt welding ⇒ edge cleaning ⇒ edge planing ⇒ forming ⇒ automatic welding ⇒ inner weld channel leveling ⇒ outer weld channel grinding ⇒ rough sizing ⇒ visual inspection of welds ⇒ in-line solution treatment ⇒ fine sizing ⇒ straightening ⇒ customized cutting ⇒ trimming end flats ⇒ radiography ⇒ downline quality inspection ⇒ hydro/gas tightness test ⇒ acid pickling and passivation ⇒ eddy current inspection ⇒ finished product inspection ⇒ marking ⇒ Weighing and storage⇒Trucking and shipping. The following diagram shows the production process of stainless steel welded steel pipe.
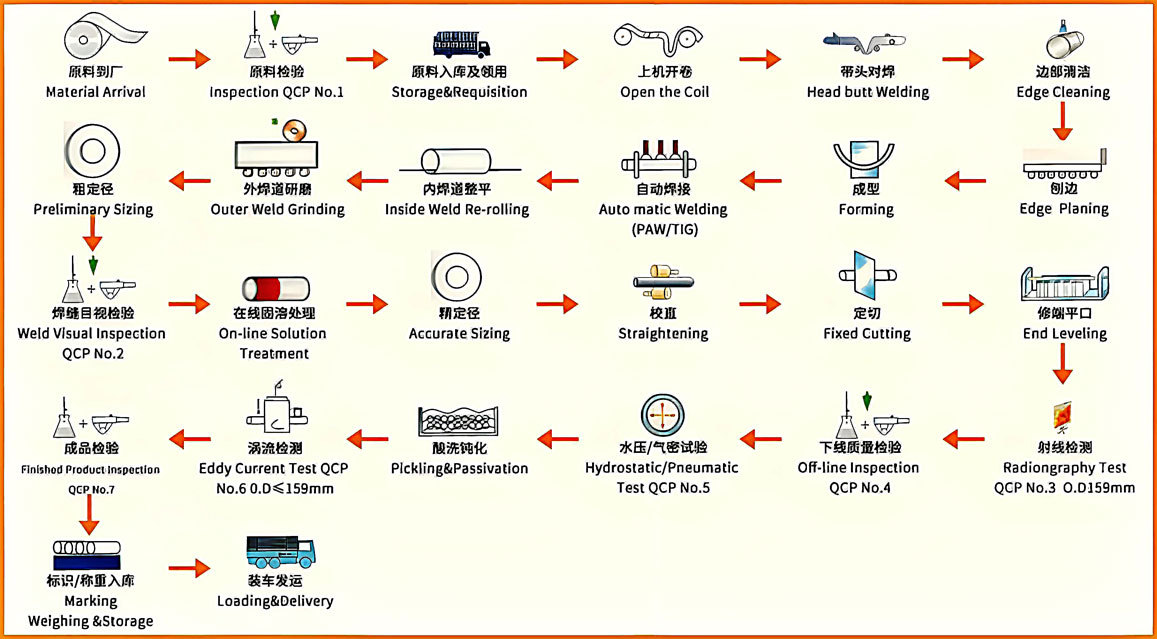
The third step, surface treatment.
Surface treatment is an important part of the production process of stainless steel pipe, which can be carried out through a variety of methods, such as mechanical polishing, chemical treatment, electrolytic polishing and so on. The main purpose is to ensure the surface finish and rust resistance of the steel pipe.
The fourth step, quality inspection
Quality inspection is an essential part of the production process of stainless steel pipe, aiming to ensure the quality and safety of steel pipe. The inspection includes the size, appearance quality, chemical composition, mechanical properties and other aspects of the steel pipe, strict requirements.
The fifth step, packaging and shipping
The last step is to package and ship the manufactured stainless steel pipe. Packaging mainly includes internal and external packaging, rust prevention measures. Shipping method according to customer requirements, can be land, sea, air and other forms. The shipping period ranges from 3-35 days.
Final Word:
Written here, I have introduced all the production process of steel pipe, if you have other insights into how the steel pipe is manufactured, welcome the global steel pipe users or steel pipe technicians to leave me a message to exchange. Understanding the manufacturing process of steel pipe can make you more aware of the performance and characteristics of each type of steel pipe, master these you can make the best use of steel pipe, play its greater role.